additional weight or drag cause major handling/ceiling problems.
Those problems are completely insignificant if weight and drag are compensated with a powerful additional thrust, as in our case. If I may remind you, the weight of the rocket engine HWK 109-509.S2 was 140 kg, but the thrust was rated at 2000 kg.
To be exact, for any sensible wing design NO increase in lift can be gained without an increase in drag…
The only problem in this otherwise theoretically completely correct statement is the word “sensible”, my dear Mr. Pdf 27. You see, if we are sufficiently willing to correlatively apply suction as an additional mean of reducing drag in our multi-slotted construction, and if deflection angle is only 10 degrees, we will be able to produce a stationary small vortex within the slot entrance. Such a vortex consumes very little energy, provided that the outlet of the slot is effectively closed. Furthermore, it has even been found possible to make the boundary layer stay completely laminar by a special design of profile, which leads to a pressure distribution favorable right to the trailing edge (with the exception of the slot itself).
Holstein and, independently, Ackeret, Rash and Pfenninger were the first to demonstrate that gains in performance, which are of completely practical value, can be realized, but the number and position of the simultaneously operated suction slots must be very carefully chosen.
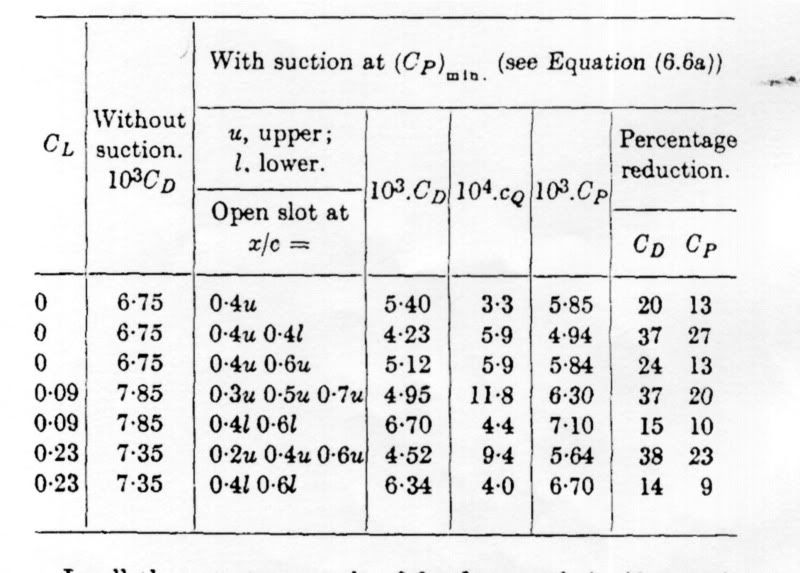
Measurements of Holstein on the Kármán-Treffz Profile 0015, with additional suction to keep the boundary layer laminar
On the other side, my dear Mr. Pdf 27, drag is - together with his companion lift! - actually a very usable assessment for our authentic purposes – significant enhancement of the combat agility, or more precisely sustained turn rate of our aircraft! You see, our favorite basic design – Ho 229 A-1 has an absolutely adequate ceiling - 15.800 meters. However, we were told that those bad and mighty B 36 bombers are able to somehow outmaneuver us up there in some kind of a dogfight… However, we will see that this assumption is utterly wrong!
Blown flaps sometimes improve the L/D, but that is if you ignore the effective loss in engine power caused by the blowing system. If you add this in (and you can easily be taking 10% of the air from the HP compressor to run the blowing system) your effective drag goes way up.
Completely artificial dilemma, my dear Mr. Pdf 27. Why you are so overwhelmed with that pitiful failure of the Hunting H.126? First of all, we have an already available direct method for missing air-mass compensation in our pockets – an afterburner. It was already envisioned in 1945 (Junkers Jumo 004 E). If properly calculated, afterburner will be able to compensate that missing air in the time of need.
On the other hand, additional methanol-water injection in those jet-exhaust gases in the very moment of need, in a minute when we are using that previously mentioned pressurized air for our flapses (while maneuvering), is completely capable to create a larger mass-flow rate as well and to compensate compressed air losses - in this way we are adding extra mass to the already existing mixture of produced gasses.
In addition, the steam that is produced is cooler, therefore additional thermal stability of the nozzle alloy is achieved too. Not even to mention that from a thermodynamic point of view that exhausting hot gas possesses a huge amount of unused heat energy, and thus a lower fuel efficiency. With our little device, a variant of the well – known MW 50 system, that problem is properly treated as well.
Of course, other possibilities are available too – engine shaft-driven rotary screw compressors, pyro-fluidic generators/amplifiers, highly pressurized pre-compressed gasses, pelleted solid-fuel thermo-jets, etc, etc. are completely available as well.
Essentially, blown flaps are NOT a solution to improving the absolute ceiling of an aircraft due to the engine power loss, which makes the effective L/D worse and hence reduces the ceiling.
Yes, my dear Mr. Pdf. You are right. But who ever talked about the absolute ceiling, if I may ask you? Ceiling of the Ho 229 A-1, as already mentioned, is excellent (yes, I know – theoretically!). The only problem emerged when we were told by you that our maneuverability actually would be a problematical subject during the battle. That is how everything started. Theoretically completely available and utterly rational solution (offered by little me) were flaps – those incredibly useful devices, capable to increase the area and chord of the wing, thereby increasing lift in critical moments of every flight - at lowered speeds, therefore in maneuvers too. They always were capable to help us with landing, takeoff, climb, and in maneuvers as well – in all those problematical conditions when our desire was to slow down a little and to still stay in the air. That’s all.
And yes - the proper use of the multi-slotted blown flapses is able to assure a victory for us in that coursed, never appropriately analyzed and provisorily fabricated aerial battle. Theory suggests that since flaps increase lift, they will increase our turn rate in the steeply banked turns as well, and those turns usually are used in every mid-air combat.
You could add an engine specifically to provide this air (indeed, there were proposals for a pressurised variant of the Avro Lancaster with a fifth engine in the bomb bay to drive a supercharger to feed air to the engines - very similar to this in concept, and probably intended as a nuclear bomb carrier if the Tube Alloys project ever came to fruition) but this adds a substantial amount of weight and the benefits probably aren’t big enough to be of any use.
Sorry, my dear Mr. Pdf 27, but that solution actually represents a complete devastation of those beautiful thrust/weight potentials. In addition, your Lancaster actually used a completely known, old solution for augmentation of the piston engine power capacity by means of additional pressurized air supply via separate compressor, driven by an Otto-cycle motor. As a matter of fact, that solution was pioneered by the USSR in 1936 with the ANT 42 prototype, and successfully followed by the French Air Force in a so called Bi-Tri moteur solution, applied in 1939 by S.N.C.A.C (Societe Nationale de Constructions Aeronautiques du Centre – previously “Farman”) on their marvelous project NC-150.
End of Part I. To be continued soon.