Oh, it always is a true pleasure when unrelated devotees of engineering are exchanging their corroborative opinions, my dear Mr. Panzerknacker. 
And yes, I am absolutely sure about those aluminum parts of the DB 507, but in the very same time you are absolutely right as well. I have to admit that this tiny misunderstanding indeed was fabricated by my personal indistinctness toward specific light aluminum alloys. As a matter of fact, much more exact and technically pertinent expression in this case should be the statement that the DB 507s crankcase, as well as the cylinder block and the cylinder heads were manufactured out of aluminum alloys. The only difference is that the engine crankcase was manufactured out of extraordinarily lightweight, cast Magnalium 30 aluminum alloy (Mg 30 %, Si 3,8%, Cu 0,8 %, Al 65,2 %), developed by renowned Dürener Metalwerke AG, Berlin-Borsigswalde. The rest of the engine – cylinder block and heads, pistons, water pump, radiator, cooling fans etc.) were fabricated out of much more ordinary Almasil, Bondur, Silumin-Gama and Duralumin alloys. 
Perhaps this is the right place for up to this time not so frequently accentuated technological fact that the cylinder heads of the renowned Maybach HL 230 gasoline engine were made out of cast iron, thus producing a noteworthy increase of engine weight. At least these parts were completely replaceable by cast aluminum alloys, and aforementioned solution was really envisioned for the next step of the German petrol engine development – notorious Maybach HL 234. However, that possibility remained unused as well…
And no, my dear Mr. Panzerknacker – unlike those notorious, but sorrowfully uninformed push-pens from the RLM, I do know that a properly conducted aluminum salvage campaign was completely able to create a net surplus of raw aluminum for that imperative engine production! According to data provided by Aluminium – Zentrale (Die Verwendung des Aluminiums in der chemischen und Nahrungsmittel –Industrie, Berlin 1942), and statements provided by E. R. Thews (Schmelztechnische verarbeitung von Altmetallen. – Wien, 1941) and E. Zurbrügg (Aluminium und seine Verwendung in der Getränke – Industrie. – Breurei Rundschau No. 6 – 7, 1944) Germany actually possessed approximately some 12.000 tons of first-grade aluminum in form of aluminum beer fermenting and storage tanks, milk transportation cans, consume salt drying cyclones, barrels for vinegar acid transportation, forks, spoons, plates, water bottles, vine bottle caps (sic!), casseroles, etc. – in a word, a completely sufficient quantity of already prepared aluminum for at least 10.000 engines of this type. After all – official statistics are clearly indicating that average per capita consumption of aluminum in 1938 was 2.64 kg in Germany, thus being surpassed only by consuming achievements of average Swiss citizen, who in those times consumed 2,85 kgs per capita. You know, if an industrial Giant like the USA was adequately prepared and prone to organize a highly successful aluminum salvage campaign that surely was obtainable in Germany too. :rolleyes:
Nevertheless, enough with this boring figures! German engineering had a couple of genuine “Vorsprung Durch Technik” solutions for heavy panzers as well.
The combination of the innovative and intrinsic quality of sadly forgotten Austrian school of engineering, combined with the generally untold proficiency of different human talents, was so technically advanced and in the very same time so different to other manufacturers, that it demanded just a little bit more research and time to be devoted by true admirers of competent engineering.
Who remembers today, my dear Mr. Panzerknacker, those sadly unknown achievements of Prof. Dr. Ferdinand Porsche, who always owed his success to air-cooled engines and truly original mechanical solutions? Not so long ago his renowned heirs decided to incorporate the doubtful innovation of a radiator and also several liters of water in every model of a car which celebrates his name. At the same time, it became necessary to fit a water pump, rubber hoses, extra seals and gaskets, and extra service items like anti-freeze, and also to limit the trouble-free use of the vehicles to the more temperate areas of the world. In those ancient times, however, engineering rationality still prevailed!
Our Gentlemen of the Old School was well aware that if certain items are not there they cannot fail, and if it they aren’t broke you don’t have to fix them. He was completely aware that there is no such thing as a water-cooled engine - there was and there is only engine that is using water as a heat-transfer medium! Therefore there was an completely logical offer: if you can cut out the Middle-man, why to hell not? And so he did just that. 
In 1942 he constructed an engine masterpiece: an 16 cylinder, supercharged, air-cooled, pre-chamber equipped, four-stroke Diesel engine with an overall displacement of 36,5 liters and a power output of 760 HP at 2500 rpm. This 2250 kg heavy, all cast-iron fabricated machine was arranged in four rows of four cylinders each, with 135° spacing between the banks.
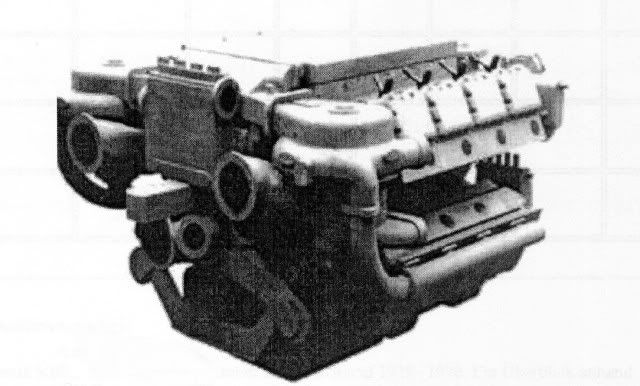
Simmering-Graz-Pauker Sla 16 (Porsche Typ 212)
Manufactured from the minimum amount of completely non-problematic materials, by economical, usual methods of production, operable at temperatures between -30 to +50 C, and unaffected by altitude, completely multi-fuel capable, and above all – much more adaptable for a truly versatile application. Manufactured out of independent, standardized four-cylinder blocks, based upon a single, 2,3 l cylinder unit, this engine represented a concept of a totally modular (Baukastensystem) and universally applicable powerplant for different vehicle classes – trucks (single block, straight 4 variant – 150 HP), half-tracks and armored cars (two blocks, V 8 320 HP variant), and X 16 option for tanks and self-propelled guns. Ease of repair and ease of placement in compact engine compartments were highlighted, as well as a significantly reduced fuel consumption due to high air surplus ratio provided by exhaust gases powered turbo-superchargers (BBC Mannheim).
Engine was completely prepared for the serial production by the Simmering-Graz-Pauker company in Wien – Florisdorf, Steyer-Daimler-Puch AG at Graz – Thondorf and envisioned for the March of 1945. Those plans never materialized, although Deutsche Nibelungenwerke in St. Valentin actually produced a single, experimental Jagdtiger, equipped with this engine.
Some additional, highly intriguing information about this issue is located here:
http://www.geheimprojekte.at/
BTW: Dr. ing. h.c. Ferdinand Porsche actually used previously mentioned modular Diesel engine concept while working in early fifties for a renowned farm machinery producing company Allgeier. Details are available here:
http://www.allcarrepair.eu/produkte/allgaier_101/allgaier_porsche_diesel_datenbuch_aller_schlepper_1305.html
Therefore these nowadays so popular, but incredibly boring complaints about “Cayenne-Diesel betrayal of glorious Porsche tradition” are completely uncorroborated.
Well, that’s all for today, my dear Mr. Panzerknacker. With this tiny essay, we have closed our “4-stroke Panzerdiesel” chapter. However, the next one will be much more interesting: as you know, two-strokers are much more intriguing, and – alas! - even less-known. But that’s why we are here…
In the meantime, as always – all the best! 